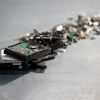
Every product eventually reaches the end of its life, so it's essential to design with this in mind, enabling recycling and reducing waste. Through years of DfR assessments on our clients' products, we’ve noticed key challenges:
- Increasing product complexity, with more diverse plastics and composites that current processes can’t handle.
- A growing trend of incorporating electronics and batteries into products like toys, which complicates recycling.
- A lack of design considerations on separating materials and accessing electronic components like PCBs.